Blow moulding
- Mech Surge
- Jun 5, 2021
- 2 min read
Blow molding is a molding process in which air pressure is used to inflate soft plastic into a mold cavity. It’s an important process for making one-piece hollow plastic component with thin walls like bottles.
Since several of those things are used for consumer beverages for mass markets production is usually organized for very high quantities.
Blow molding is accomplished in two steps. These are
Fabrication of a starting Tube of molten plastic referred to as parison.
Inflation of the tube to the specified final shape. Forming the parison is accomplished by either of two processes extrusion or injection molding.
EXTRUSION BLOW MOLDING
In most cases, the method is organized as a very high production operation for creating plastic bottles. The sequence is automated and typically integrated with downstream operations such as bottle filling and labeling.
It is typically a requirement that the blown container be rigid, and rigidity depends on wall thickness among alternative factors.
Steps followed in extrusion blow molding are
Extrusion of parison
Parison is pinches at the top and sealed at the bottom around a metal blow pin as the two halves of the mold come together.
The tube is inflated so that it takes the shape of the mold cavity.
Mold is opened to remove the solidified part.
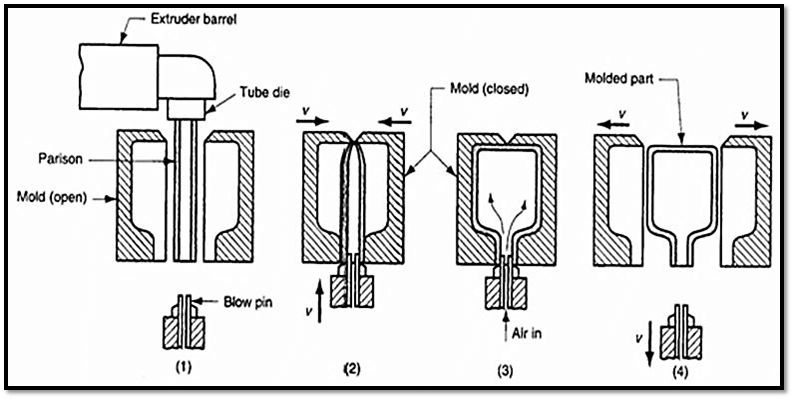
INJECTION BLOW MOLDING
In this method, the starting parison is injection molded instead of extruded. A simplified sequence is outlined in below.
Compared to its extrusion based competitor the injection blow-molding process has a lower production rate.
Steps followed in Injection blow molding are
Parison is injection molded around a blowing rod.
Injection mold is opened and parison is transferred to a blow mold.
Soft polymer is inflated to conform to a blow mold.
Blow mold is opened and blown product is removed.

STRETCH BLOW MOLDING
In a variation of injection blow molding referred to as stretch blow molding. the blowing rod extends downward into the injection molded parison throughout step.
Therefore stretching the soft plastic and creating a more favorable stressing of the polymer than conventional injection blow molding or extrusion blow molding.
The resulting structure is more rigid with higher transparency and better impact resistance. The most widely used material for stretch blow molding is polyethylene terephthalate (PET).
Stretch blow molding steps are
Injection molding of the parison
Stretching
Blowing

Comments