Cupola furnace
- Mech Surge
- May 31, 2021
- 4 min read
A cupola may be a vertical cylindrical furnace equipped with a tapping spout neat its base.
Cupolas are used for melting cast irons. It consists of a large shell of steel plate lined with refractory.
The charge, consisting or iron, coke, flux and possible alloying elements, is loaded through a charging door located less than halfway up the height of the cupola.
The iron is typically a mixture of pig iron and scrap.
Coke is that the fuel used to heat the furnace. Forced air is introduced through openings near the bottom of the shell for combustion of the coke.
The flux may be a basic compound like limestone that reacts with coke ash and other impurities to form slag.
The slag serves to cover the melt protecting it from reaction within the environment inside the cupola and reducing heat loss.
As the mixture is heated and melting of the iron occurs the furnace is periodically tapped to provide liquid metal for the pour.
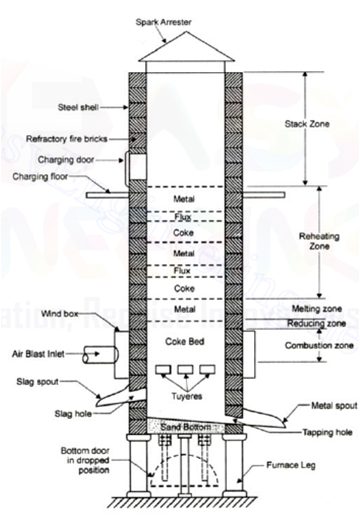
COMBUSTION OR OXIDIZING ZONE :
It is the zone where combustion takes place. It extends from the top of the tuyers to a surface boundary below that all the Oxygen of air is consumed by combustion.
The temperature is about 1800°C.
C(coke) + O2 (from air) ~ CO2 + Heat
REDUCING ZONE :
It extends from the top of the combustion zone to the top of the initial coke bed. The CO2 produced in the combustion zone moves up and reduced to CO.
The temperature also drops to 1650°C.
CO2 + C2 ~ CO – Heat
MELTING ZONE :
It includes primary layer of pig iron above the initial coke bed. In this zone the pig iron is melted.
3 Fe + 2 CO ~ Fe3C + CO2
PRE HEATING ZONE :
It includes all the layers of cupola charges placed above the melting zone to the top of the last charge.
Layers of charges are heated by the out-going gases. The temperature in the zone is upto 1050°C.
STACK :
It is the zone beyond the pre-heating zone through that the hot gases go to the atmosphere.
CONSTRUCTION & WORKING :
The cupola consists of a cylindrical steel shell lined on the inside with refractory bricks.
The entire structure is supported on legs and is open at top and bottom when not in use.
At the bottom doors are provided which can be closed and propped to prepare a hearth for burning coke.
About 100 mm above the bottom of the shell is an opening called the tap hole with a projecting spout for taking out the molten metal.
On the rear of the tap hole may be a slag hole to drain out slag. It is about 50 to 150 mm above the level of the tap hole.
This height may be less if the cupola is fitted with a receiver and the metal is continuously drained form the cupola.
About 50 to 150 mm above the slag hole are openings through the shell into the cupola shaft called tuyers.
These openings permit a blast of air from a wind box surrounding the cupola shell around the tuyers.
These tuyers are provided around the shell in one or more rows to provide a balanced supply of air.
Air is supplied into the wind box from a blower through pipes.
The cupola shaft extends further up from the wind box to a charging platform.
The height of the cupola from the tap hole to the charging platform is called the effective height.
It is about 4 to 6 times the internal diameter of the cupola for small and medium size cupolas and about 3 to 5 metre for larger ones.
The cupola shaft extends further up by another 3 to 5 metre to give a chimney effect for natural draft.
The total tuyers area is 15 to 25 percent of the cupola melting area. The wind belt section is about 30 percent of cupola melting area and so on.
Commercial cupola sizes vary from 450m to over 2000m in inside diameter with melting capacities ranging from 1.5 to 35 tonnes per hour.
The cupola furnace has several unique characteristics which are responsible for its widespread use as a melting unit for cast iron.
The cupolas is one of the only methods of melting which is continuous in its operation.
High melt rates
Relatively low operating costs
Ease of operation
The construction of a conventional cupola consists of a vertical steel shell which is lined with a refractory brick.
The charge is introduced into the furnace body by means of an opening approximately half way up the vertical shaft.
The charge consists of alternate layers of the metal to be melted, coke fuel and limestone flux.
The fuel is burnt in air which is through tuyeres positioned above the hearth. The hot gases generated in the lower part of the shaft ascend and preheat the descending charge.
Most cupolas are of the drop bottom type with hinged doors under the hearth which allows the bottom to drop away at the end of melting to aid cleaning and repaired.
At the bottom front is a tap hole for the molten iron at the rear positioned above the tap hole is a slag hole. The top of the stack is capped with a spark arrester hood.
A typical operation cycle for a cupola would consist of closing and propping the bottom hinged doors and preparing a hearth bottom.
The bottom is usually made from low strength moulding sand and slopes towards a tapping hole.
A fire is started in the hearth using light weight timber. Coke is charged on top of the fire and burnt by increasing the air draught from the tuyers.
Once the coke bed is ignited and of the required height alternate layers of metal, flux and coke are added until the level reaches the charged doors.
The metal charge would typically consist of pig iron, scrap steel and domestic returns.
An air blast is introduced through the wind box and tuyers located near the bottom of the cupola. The air reacts chemically with the carbonaceous fuel thus producing heat of combustion.
Soon after the blast is turned on molten metal collects on the hearth bottom where it is eventually tapped out into a waiting ladle or receiver. As the metal is melted and fuel consumed additional charges are added to maintain a level at the charging door and provide a continuous supply of molten iron.
At the end of the melting campaign charging is stopped but the air blast is maintained until all of the metal is melted and tapped off.
The air is then turned off and the bottom doors opened allowing the residual charge material to be dumped.
Comments