Gas tungsten arc welding or tungsten inert gas welding (TIG)
- Mech Surge
- Jun 1, 2021
- 3 min read
Tungsten Inert Gas (TIG) or Gas Tungsten Arc (GTA) welding is the arc welding process.
In this welding arc is generated between non consumable tungsten electrode and work piece.
The tungsten electrode and the weld pool are shielded by an inert gas normally argon and helium.
The tungsten arc method is utilized widely for the precision joining of critical components which require controlled heat input.
The small intense heat source provided by the tungsten arc is ideally suited to the controlled melting of the material.
Since the electrode is not consumed during the process welding without filler material may be done without the need for continual compromise between the heat input from the arc and the melting of the filler metal.
As the filler metal when required can be added directly to the weld pool from a separate wire feed system or manually all aspects of the process can be precisely and independently controlled.
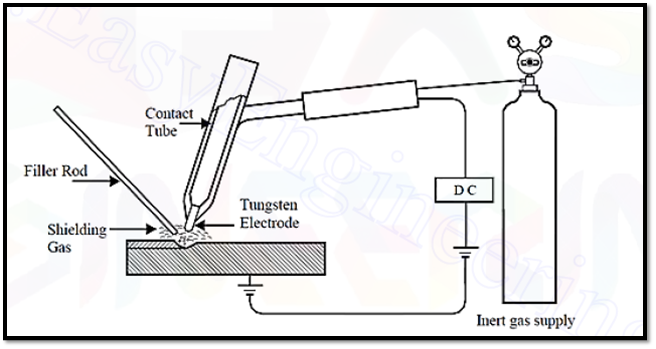
The arc is ignited by high voltage, high frequency pulses or by touching the electrode to the work piece.
Selection of Electrode :
D.C.Welding : 1 or 2 % of thoria. Thoria helps to improve electron emission which facilitates easy arc ignition.
A.C.Welding : Pure tungsten or tungsten-zirconia. Tungsten electrodes are commonly available from 0.5 mm to 6.4 mm diameter and 150 - 200 mm length.
The current carrying capacity of each size of electrode depends on whether it is connected to negative or positive terminal of DC power source.
AC is used only in case of welding of aluminum and magnesium and their alloys.
The capacity to limit the current to the set value is equally crucial when the electrode is short circuited to the work piece. Open circuit voltage of power source ranges from 60 to 80 V.
SHIELDING GASES :
Argon
Argon + Hydrogen
Argon/Helium
Helium is generally added to increase heat input. Hydrogen will result in cleaner looking welds and also increase heat input. However, Hydrogen may promote porosity or hydrogen cracking.
Argon or helium may be used successfully for most applications with the possible exception of the welding of extremely thin material for which argon is essential.
Argon generally provides an arc which operates more smoothly and quietly is handled more easily and is less penetrating than the arc obtained by the use of helium.
For these reasons argon is usually preferred for most applications, except where the higher heat and penetration characteristic of helium is required for welding metals of high heat conductivity in larger thicknesses.
Aluminum and copper are metals of high heat conductivity and are examples of the type of material for which helium is advantageous in welding relatively thick sections.
Pure argon can be used for welding of structural steels, low alloyed steels, stainless steels, aluminum, copper, titanium and magnesium.
Argon hydrogen mixture is used for welding of some grades of stainless steels and nickel alloys. Pure helium may be used for aluminum and copper.
Helium argon mixtures may be used for low alloy steels, aluminum and copper.
BENEFITS :
Superior quality welds
Welds can be made with or without filler metal
Precise control of welding variables (heat)
Free of spatter
Low distortion
LIMITATIONS :
Requires greater welder dexterity than MIG or stick welding
Lower deposition rates
More costly for welding thick sections.
APPLICATION :
during welding of thick pipes but is widely being used for welding of thin walled pipes and tubes. It is used for precision welding in nuclear, aircraft, chemical, petroleum, automobile and space craft industries. Aircraft frames and its skin, rocket body.
Comments