Investment castings
- Mech Surge
- May 21, 2021
- 2 min read
The investment casting method begins with the production of wax replicas of the specified castings. These replicas referred to as patterns. These are injection molded in metal dies. A pattern should be manufactured for every casting to be produced.
A number of pattern are attached to a central wax persist to form a casting cluster.
After some initial pre-dips that thoroughly clean the wax, the assemblies are immersed into a liquid ceramic slurry and then into a bed of very fine sand to form a shell.
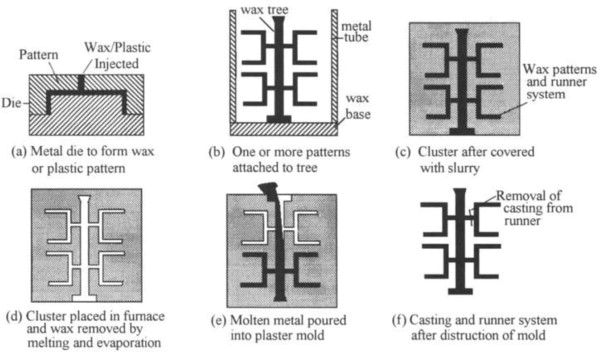
The first essential layers are typically applied by hand between every layer the ceramic is allowed to dry.
The later heavier layers are typically applied by automated equipment or special shell building robots.
Enough layers should be applied to build a shell strong enough to withstand subsequent operations. When the shell is totally dry the wax is melted out in a high pressure steam autoclave leaving a hollow void within the mold which exactly matches the shape of the assembly.
Prior to casting the shells are fired in an oven where intense heat burns out any remaining wax residue and prepares the mold for the molten metal.
In the conventional gravity pouring method, metal is poured into the shell through a funnel shaped pour cup and flows by gravity down the sprue channel through the gates and into the part cavities.
As the metal cools the elements, gates, sprue and pouring cup become one solid casting. After the casting has cooled the ceramic shell is broken off and the parts are cut from the sprue using a high speed friction saw.
After minor finishing operations the castings which are identical in configuration to the wax patterns which shaped them are ready for certification and shipment to the customer.
ADVANTAGES :
Parts of great complexity and intricacy can be cast.
Close dimensional control and good surface finish.
Wax can usually be recovered for reuse.
DISADVANTAGES :
Many processing steps are required.
Relatively expensive process.
Comments