Fluidized bed combustion (FBC) boiler
- Mech Surge
- Apr 21, 2021
- 4 min read
Principle of FBC
When a gas is passed through a packed bed of finely divided solid particle, it experiences a pressure drop across the bed. At low gas velocity, the pressure drop is tiny and not disturbs the particles. However if the velocity is increased further, A stage is reached, once particles are suspended within the gas stream and therefore the packed bed becomes a fluidized bed. With more increase in velocity the bed becomes turbulent and rapid mixing of particle occurs. In general, the behavior of this mixture of solid particles and gas is like fluid. Burning of a fuel in such state is thought as fluidized bed combustion.
Classification of FBC
Atmospheric fluidized bed combustion (AFBC)
Bubbling fluidized bed combustion (BFB)
Circulating fluidized bed combustion (CFB)
ressurized fluidized bed combustion (PFBC)
As the fluidizing velocity is increased, smaller particles are entrained in the gas stream and transported out of the bed.
The bed surface, well-defined for a BFB combustor becomes more diffuse and solids densities are reduced in the bed.
A fluidized bed that is operated at velocities in the range of 4 to 7 m/s is referred to as CFB.
Bubbling fluidized bed combustor
At low fluidizing velocities (0.9 to three m/s) comparatively high solids densities ar maintained within the bed and solely alittle fraction of the solids ar entrained from the bed.
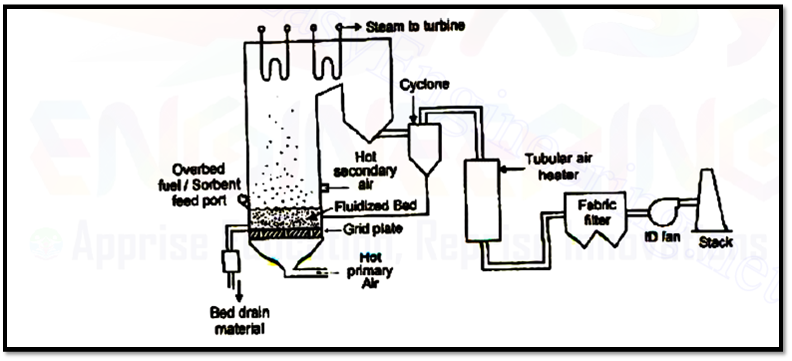
Fuel and sorbent are introduced either above or below the fluidized bed. The bed consisting of about 97% limestone or inert material and 3% burning fuel, is suspended by hot primary air getting into the bottom of the combustion chamber.
The bed temperature is controlled by heat transfer tubes immersed within the bed and by varying the quantity of coal in the bed.
As the coal particle size decreases, as a results of combustion or attrition, the particles are elutriated from the bed and carried out the combustor.
A portion of the particles elutriated from the bed are collected by a cyclone collector down-stream of the convection pass and returned to the bed to enhance combustion potency.•Secondary air will be added further in the bed to enhance combustion potency and to attain staged combustion, therefore lowering NOx emissions.
Most of the first BFBs used tubular air heaters to reduce air leakage that might occur as a results of comparatively high primary air pressures needed to suspend the bed.
Circulating fluidized bed combustor
In a CFB, primary air is introduced into the lower portion of the combustor, wherever the heavy bed material is fluidized and maintained.
The upper portion of the combustor contains the less dense material that’s entrained from the bed.
Secondary air generally is introduced at higher levels within the combustor to confirm complete combustion and to reduce Nox emissions.
The combustion gas generated within the combustor flows upward with a considerable portion of the solids inventory entrained. These entrained solids are separated from the combustion gas in hot cyclone-type dust collectors or in mechanical particle separators, and are continuously returned to the combustion chamber by a recycle loop.

The combustion chamber of a CFB unit for utility applications usually consists of membrane-type welded water walls to provide most of the evaporative boiler surface.
The lower third of the combustor is refractory lined to protect the water walls from erosion within the high velocity dense bed region. Many CFB design offer external heat exchangers, which are unfired dense BFB units that extract heat from the solids collected by the dust collectors before it’s returned to the combustor.
The external heat exchangers are used to provide further evaporative heat transfer surface additionally as superheat and reheat surface, depending on the manufacturer’s design.
The flue gas, after removal of more than 99% of the entrained solids in the cyclone or particle separator, exists the cyclone or separator to a convection pass.
The convection pass designs are similar to those used with unconventional coal-fueled units, and contain economizer, superheat, and reheat surface as required by the application.
Pressurized Fluidized Bed Combustion
The PFBC unit is classified as either turbocharged or combined cycle units.
In turbocharged arrangements combustion gas from the PEBC boiler is cooled to approximately 394° C and is used to drive a gas turbine.
The gas turbine drives an air compressor, and there is little, if any, net gas turbine output. Electricity is produced by a turbine generator driven by steam generated in the PFBC boiler.
In the combined cycle arrangement, 815°C to 871°C combustion gas from the PFBC boiler is used to drive the gas turbine. About 20% of the net plant electrical output is
provided by the gas turbine. With this arrangement, thermal efficiency 2 to 3
percentage points higher than with the turbocharged cycle are feasible.
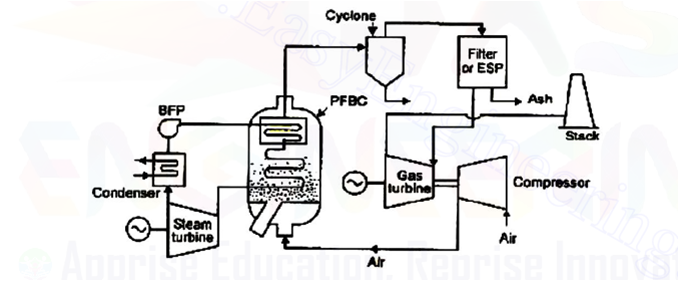
Advantages of fluidized bed combustion
SO2 can be removed in the combustion process by adding limestone to the fluidized bed, eliminating the need for an external desulfurization process.
Fluidized bed boilers are inherently fuel flexible and, with proper design provision, can burn a variety of fuels.
Combustion FBC units take place at temperatures below the ash fusion temperature of most fuels. Consequently, tendencies for slagging and fouling are reduced with FBC.
Because of the reduced combustion temperature, NOx emissions are inherently low.
Comments